An expert perspective on global supply chain and food safety culture
Guest writers from BRCGS share their insights on how culture helps to improve food safety and enhances prospects of passing audits
2 March 2023
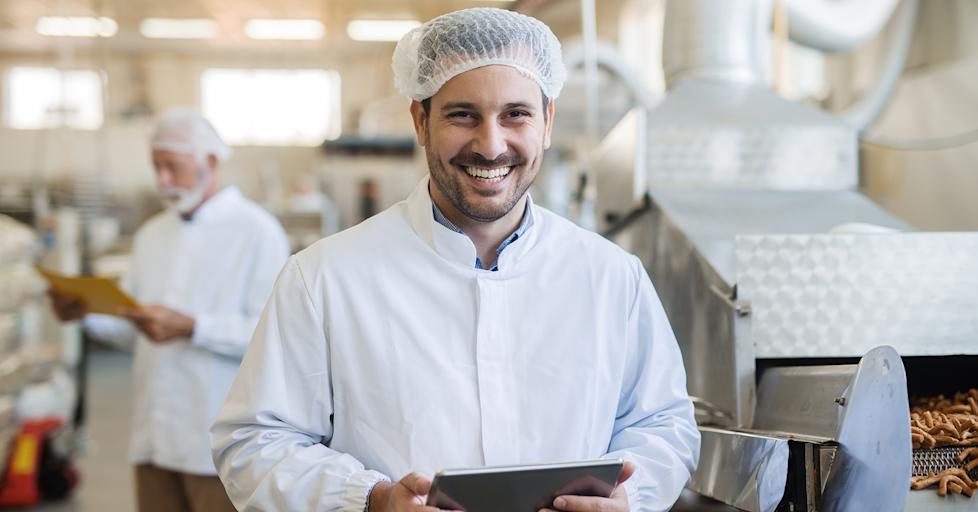
Share this article
In this article, Angela O’Donovan and Paul Munday, provide an update from the perspective of BRCGS on food safety culture. It will highlight the changes that BRCGS has made to food safety culture in Food Safety Issue 9, updated in August 2022. In addition, we will give you practical recommendations to implement a stronger food safety culture.
Food safety culture improves performance for food operators
This is important because food safety culture has been proven to enhance the performance of food safety across a number of KPIs. For example, a study by Brunel University found that 10.9% of food waste was caused by human error. But the Institute of Food Science and Technology research discovered that there were 54% less errors in businesses that have a strong company culture.
In addition to the business benefits, there is a chance it can help food operators prepare for the BRCGS audit too. In a survey to sites that performed the Food Safety Culture Excellence assessment, 89% of respondents said it helped reduce non-conformities.
How food safety culture has changed Food Safety Issue 9
Angela O’Donovan, BRCGS Head of Standards
The first thing I want to highlight is that BRCGS believe food safety culture is essential for an effective food safety management system to be successful. As outlined above, it helps mitigate risk for food operators and ultimately helps to protect consumers. It is so important that we put it on the first page of our requirements, in every Standard.
Whilst culture is a fundamental requirement in clause 1.1 it also appears in several other clauses too. Why do I mention this? Well, to provide some perspective, in our previous Standard (Food Safety Issue 8) culture was only mentioned once, in clause 1.1.2.
In addition to this, additional requirements in the culture clause indicate how it has been enhanced. The image shows[AO1] [BC2] a page directly from Food safety issue 9, clause 1.1.2 – all of the text in red is new.

These key changes to food safety culture since Food Issue 8 give sites more direction on what is required to achieve a positive culture at their sites.
The new Standard still insists senior management are committed because experience has shown us that only where senior management are fully committed to the food safety processes can sites consistently achieve a good food safety culture. This requires senior management to write this commitment into a company policy and share with all staff – everybody from the top down should be clear on what the company plan to do to manage food safety culture.
Practical steps to improve food safety culture
So, what does this top-down approach look like?
It starts with having a plan to measure what is needed to achieve a positive culture change, as it affects everyone on site. We suggest you document it so that it is easier to demonstrate what you plan to do. Not only will this help communicate your intentions to auditors, it also makes it easier for you to identify, measure and track progress. We do not dictate how to go about this but we have provided a minimum scope for your plan.
Examples are activities around:
clear and open communication on product safety
training for staff for food safety
feedback from employees - such as surveys or the BRCGS Culture Excellence Module
the behaviours required to maintain and improve product safety processes
performance measurement and so on.
The timeline for the plan can be as long or as short are you need, it can extend up to 5 years if necessary, however it does needs to be reviewed and updated at least annually.
Taking all this into account, let’s see how a site could develop its communication to staff to improve culture. For example, communication within a site is sometimes only finance related and might not mention anything about product safety. Or perhaps a site may only be communicating to staff on revenue performance, inventory turnover, the amount of waste product, etc. Whilst these KPIs are important they do not directly relate to improving a food operator’s food safety culture. Focussing on business outcomes only may lead staff to mistakenly believe that product safety is not important.
Therefore, future communications to staff could include for example the number/trends for customer complaints received each period, percentage of defects found and rectified, corrective actions implemented, internal audits completed or product safety related objectives. Then, the business could set up formal channels for staff to report issues relating to these KPIs. Using this information, the site could develop its food safety culture plan and provide training to staff.
In turn, this approach may see improvements on future communications to staff and also help improve the moral and staff engagement, at the site. And whilst I make that last point, it’s important to note that BRCGS auditors will not audit the culture of the site itself. They are simply looking for evidence that a culture plan exists and is being implemented effectively.
BRCGS learnings on food safety culture from audit data
The effect of the new culture requirements in the Food Safety Issue 9 Standard are yet to be identified – the updated standard was only released in August last year and audits began on 1st February this year. However, non-conformance data from over 20,000 sites for issue 8 is available, and we can say that non-conformities against clause 1.1.2 were consistently one of the most commonly occurring.
We have some ideas what might be causing this.
Don’t just plan culture, integrate it into the operation
We believe that sites sometimes look at clause 1.1.2 in isolation, as in “have we got a plan in place?” Whilst there is definitely a need to ensure there is a plan, it must be emphasised that improvement of culture should be imbedded into business as usual. We have tried to reflect this point by adding references to culture into some of the other clauses e.g. 1.1.1 and 1.1.4 – Management Review Meetings.
Linked to this is that the food safety culture clause is dual coloured, which means that the auditor will want to see a plan and appropriate records. In addition, they will also be looking to see evidence of how it is implemented throughout the site. For example, in production – how has the site implemented the culture plan, how have they communicated it, what reporting mechanisms do they have in production etc.
Audit trends show sites fail to take all food safety culture points into account
In addition to the previous points, we can also see the impact of culture on food safety data. We analysed non-conformity trends and their root causes, which showed the most common reason was that sites failed to consider all the points in the clause and it was, therefore lacking content.
I am sure it would be disappointing for any site if they received non-conformities for their first Food Safety Issue 9 audit, simply because they didn’t update their plan to reflect the new additions. Obviously, the clause also requires the implementation of the plan. Therefore, there will need to be evidence of anything already implemented or a plan of when future activities will start.
Failure to review the culture plan was also a cause of non-conformities in Issue 8. There is an opportunity to address this, whilst updating for Issue 9, for example you could do a single review that combines what went well, what didn’t and what's new for Issue 9. And as many sites also consider their budgets at this time of year, perhaps this is an ideal time to think about new opportunities for your culture requirements and budget for them now.
Don’t forget the basics of product safety
Whilst culture has greater emphasis, it will be even more critical to ensure the day-to-day activities, or the basics, are managed appropriately as part of the culture plan. It shouldn’t be forgotten that product safety culture seeks to build on the underlying and fundamental attitudes that are vital for good implementation of other systems within the site.
There are many tools available to support companies. The Culture Excellence Module is a great product for sites who struggle to evaluate where to focus their activities and where they can have most impact. However, sites must not forget they will still need to build the results into a plan and implement the activities to meet the full requirements of the clause.
One requirement that is not clearly written into the BRCGS Standard but is clearly evident from our experience talking with food operators is the fun they have had implementing their food safety culture plans. Because it is an inclusive process, requiring input from the entire business, it provides an opportunity to build moral and bind your team together. So, please don’t forget to have lots of fun, celebrate success and enjoy celebrating together – all of this drives a very positive culture also.
Adoption of culture planning and reporting is growing in the food industry
Paul Munday, Global Head of Commercial Sales for BRCGS & Culture Excellence
In our conversations with clients who adopt the Food Safety Culture Excellence (FSCE) survey, we know that food safety culture is becoming an integral part of food operators’ processes and planning. From our experience, we have seen an explosion of sites utilising FSCE, which has been driven by the growth in organisations that understand the importance of culture on food safety and the positive impact this approach can have on a business KPIs.
Our customers tell us that when they listen to their staff, they get a real picture of what is really going on day to day. This has numerous benefits.
Staff feel they have a voice (anonymous) which means they can be honest (which is backed up by data)
Everyone is involved across the business – meaning that culture is getting stronger internally
Identifying areas to improve or focus on
Enhanced brand – what a place to work
Benchmarking across the business and sectors – healthy competition
Understanding root cause
Insight for the business
Staff retention
Output of culture focus – team building, everyone involved, rewards, companywide initiatives, healthy competition, knowledge, better products or solutions
Training support – focus on what is needed and where
All parts of business internal or external get involved (full time staff to agency staff)
Reviewing this year on year so you can see improvements
All of the above feeds into the bottom line of the business
As you can see from the above, adopting an approach to culture will not only help with food safety but can benefit the overall business.
What is really telling right now, compared to 2-3 years ago is, food safety culture is now a common discussion, with organisations on the second and third culture assessment cycle. This shows that sites, whether large or small, are seeing benefits that are helping to drive continuous improvement.
Improve food safety culture in your operation
Developing a strong food safety culture takes an expert approach. You can discover how to do it at BRCGS.
Find out more
Angela O’Donovan, BRCGS Head of Standards
Angela joined BRCGS in January 2021 as Head of Standards. She is responsible for ensuring BRCGS deliver the standards our specifiers and customers want, that they are aligned to the needs of the market and are consistent in product design and their approach to brand protection.
Angela has 30 years experience in safety, quality, legality, ethical and sustainability, in both food and consumer goods industries. She has worked in high risk manufacturing, was Head of QA at Woolworths, Head of QA Mothercare, Director of Quality Wessanen UK, NL & Germany, Director of Technical Services for Bidfood where she established and led their Safety, Packaging and Product Sustainability vision for over 16,000 sku’s alongside maintaining their Storage and Distribution certification.
View Profile
Paul Munday, Global Head of Commercial Sales for BRCGS & Culture Excellence
Paul has 15+ years experience working with global standards for certification, verification and business improvement. Living and working in multiple locations from Italy, Spain, Switzerland and Austria to Dubai and the USA, he has gained wealth of experience working across multiple cultures and regions, which has helped to shape how he works today.
Paul spends a lot of his time with his wife and rescue dog Moses, planning adventures and travelling, alongside his passion for Trail and Ultra Running.
View ProfileShare this article